阻燃输送带粘合强度影响因素分析
阻燃输送带粘合强度影响因素分析
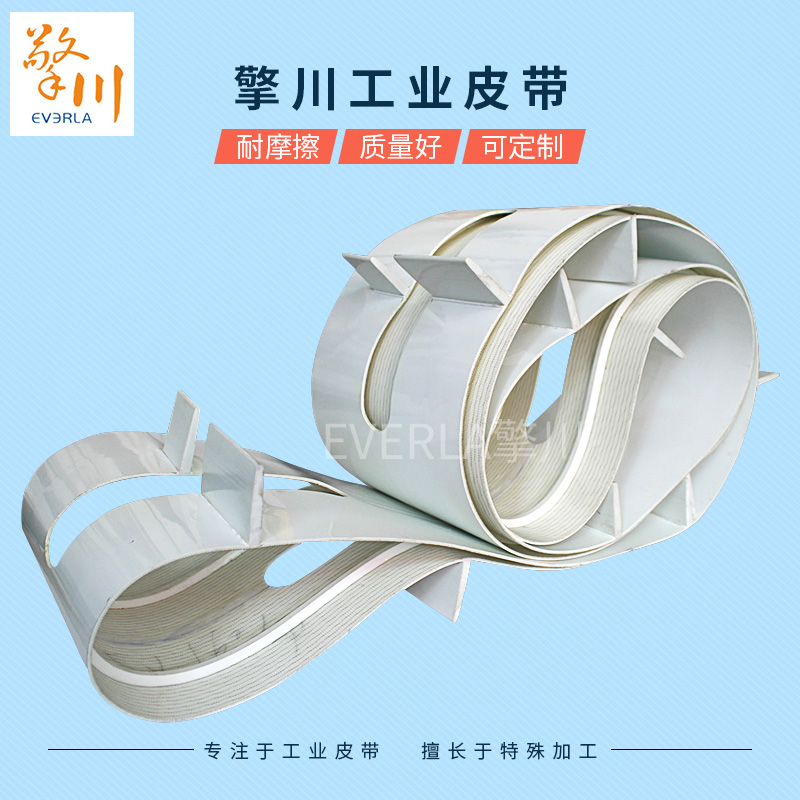
橡胶面整芯阻燃输送带系列产品中,其性能价格比高,适应性广,维修更换方便等诸多特点,被许多煤矿优先选用为井下煤炭运输载体。美中不足的是,部分生产厂家的产品在使用过程中容易出现包皮与带芯分离的现象,俗称“剥皮”或“剥皮”。作者在多年的生产实践中,结合售后服务经验,对橡胶面整芯阻燃输送带覆盖层与芯层之间粘合强度的影响因素进行了研究。通过正交实验,研究了胶粘强度在生产过程中的影响因素,包括胶粘温度、胶芯浸胶量、胶粘速度、胶芯含棉量、棉纱质量、胶粘胶胶胶比、胶包层温度场、胶包层与胶芯粘接时胶粘剂的粘接性能等,找出了影响胶包层粘接性能的主要因素,并对胶包层在使用过程中出现的一些问题作了初步分析。
覆盖层与芯层之间粘结强度的物理意义。
在煤矿用织物整芯阻燃输送带(MT914—2008)标准中,对粘结强度的定义是,在进行覆盖胶剥离试验时,每毫米宽度的整块试样承受的拉力。换句话说,包覆层和芯层之间的粘合强度主要是通过测试每毫米厚度包覆层和芯层之间的剥离阻力来计算的。强力试验机在剥离过程中产生的拉力和阻力是一对平衡力,方向相反,大小相等。
第二部分,生产过程的影响因素。
通过对粘合强度的检测可以看出,在包芯层剥离过程中,不仅有包芯层和芯层表面的塑化糊分离,而且包芯层和芯层内部的塑化糊分离,甚至还有芯层表面的棉纱撕裂。在分析了橡胶面整芯阻燃输送带生产工艺的基础上,提出了胶包层与芯层之间粘合强度的大小与胶包层塑化温度、胶包层浸润量、塑化速度、胶包层含棉量、棉纱质量、胶包层橡塑比、胶包层贴合温度场等因素有关。这些因素中,塑化温度、塑化速度决定了“浸浆带芯”的塑化程度,带芯含棉量、棉纱质量、浸浆带芯的浸浆时间和浸浆充分度.包覆层“橡塑比”和橡胶的种类决定了包覆层与包覆层表面PVC塑化糊的融合度。
一、浸糊带芯的塑化度。
型芯的塑化度不仅对整芯阻燃胶带的整体使用效果有很大影响,而且对型芯与型芯之间的粘接强度也有重要影响。唯有塑化充分,PVC塑化胶在芯层中才能与骨架(涤纶丝、尼龙丝和棉纱)结合在一起,从而使包覆层与芯层之间具有一定的粘合力。实验证明当其它影响因素相同时.塑化度越大,粘合强度越高。相反的,越小越好。要特别强调的是,浸糊带芯的“过塑化”将使粘结强度显著降低。
二、带芯浸膏的充分程度。
前面已经说过,带芯浸膏的量、含棉量、棉纱质量决定了带芯浸膏的充分度,它对制品阻燃性能的影响很大,但对粘接性的影响不大,只是带芯层表面的浸膏量对粘接强度的影响很大。面糊量大时,包覆层只能与PVC塑化糊结合,棉芯层与棉纱的粘接作用无法发挥;面糊量小时,尽管包覆层能与棉纱结合,但与棉纱的粘接程度降低。实验结果表明,由于包覆层的表面浸糊量太小或太大,导致包覆层与芯层之间的粘结强度下降。
三、包覆层和芯层PVC塑化糊的粘合度。
无论是塑料面芯阻燃输送带,还是橡胶面芯阻燃输送带,其骨架均由浸渍PVC糊料的整体带芯塑化而成,区别在于两者的包皮材料是塑料胶料和橡塑胶料混合而成。塑胶材料以PVC粉末树脂为主成分,并加入增塑剂、阻燃剂及其他配合剂,与芯层表面的PVC塑化糊在分子结构上属同一物质,粘合效果自然良好。橡胶共混料是在一定工艺条件下,与塑料、阻燃剂、增塑剂、硫化剂等各种配合剂共混而成的一种橡胶制品,其溶度参数与PVC的相似程度直接决定了其包芯层与PVC塑化糊的融合程度。如果选择的是与PVC溶解度参数相似(即相容性较好)的橡胶(例如NBR),加上良好的共混效果,则制得的橡塑共混胶料与芯层的共混程度接近。通过生产实践和试验结果表明,当采用相容性较好的橡胶时,包芯层与芯层之间的粘合强度基本达到塑胶面整芯阻燃输送带的水平,而当采用相容性较差的橡胶时,粘合强度明显降低。热塑弹性体是介于塑料和橡胶之间的一种复合材料,与橡胶和塑料都具有良好的粘合性能,如橡胶面整芯阻燃输送带的包覆材料选择了橡塑共混的热塑性弹性体,其包覆强度与芯层之间较高。我国一家企业是第一个采用该技术生产产品的。包芯与包芯之间的粘结强度超过10N/ram,达到国际先进水平。这项新技术值得在国内同行推广应用。
四、包覆层与芯层结合时的温度场。
该包覆层与塑化带芯粘合时的温度场,是指包覆层与塑化带芯挤压贴合时的环境温度。由于塑化带芯表面的PVC熔融挤压粘结在覆盖层上,冷却后粘结效果最佳.因此,有必要提供接近于此的温度场。在国内现有的橡胶面整芯阻燃输送带生产工艺中,挤出式贴胶比传统硫化式贴胶具有明显的优势。这主要是由于硫化贴胶工艺所提供的温度场不能达到PVC在塑化带芯表面熔化的状态。如果硬要提高硫化机的平板温度,与平板直接接触的橡塑共混胶包层极易发生老化、降解现象。严重者还会导致提前焦烧,这样反而会降低包芯与包芯之间的粘结性能。
使用过程中的影响因素分析。
输送带在使用过程中,输送距离过短,选择和调整不当,遇到硬物撞击和滚筒直径过小等问题,都会对输送带覆盖层和芯层之间的动态粘结强度产生不利影响。输送距离过短:单位时间内输送带通过滚筒的次数增加,带体发生曲挠的频率也随之增加,使输送带覆盖层和芯层的粘接性能逐渐下降。清扫设备选配调整不当:输送带与清扫设备之间容易嵌入矸石等尖端材料,矸石与输送带在移动过程中产生摩擦,容易产生输送带覆盖层局部破损、脱层。硬碰撞:如果装载点落差太大,矸石、钢钎等硬碰撞从高处撞击到输送带表面,将严重降低覆盖层与芯层之间的粘结强度,造成碰撞处出现脱层。有时在表面上很难观察到,经过一定时间的运转和曲挠作用后,出现脱层现象。转鼓直径过小:若输送带转鼓直径过小,会加剧输送带带体内的曲挠作用,破坏输送带覆盖层与芯层之间的粘结分子结构,加速剥离,从而提前产生输送带覆盖层脱层,缩短输送带的使用寿命。