橡胶输送带的硬化
橡胶输送带的硬化
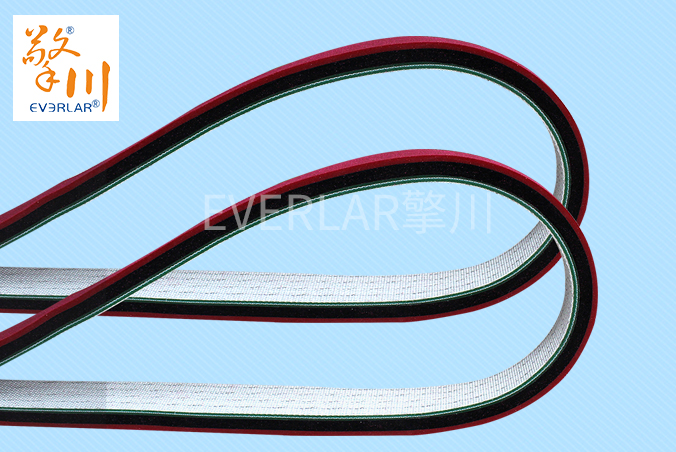
对胶带硫化工艺的认识,主要是掌握硫化的本质及其影响因素,硫化条件的确定与实施,硫化设备的操作方法,硫化设备的结构,其中硫化是在一定温度、时间和压力下,混炼胶线大分子进行交联,形成三维网状结构的过程,硫化使橡胶的塑性降低,弹性增加,抗外力变形能力大大提高,同时也改善了橡胶的其它理化性能,成为有应用价值的工程材料。
硫是橡胶制品加工的最后一道工序,硫化物的质量对硫化胶的性能有很大的影响,严格掌握硫化条件,硫化机两热板的受压表面应彼此平行,热板采用蒸汽加热或电加热,平板在整个硫化过程中,所受压力不小于三兆帕,热板中心点的最大温差不大于零点五度,常用技术规格为最大闭合压力200吨,柱塞最大行程为200毫米,平板面积为500×500,工作层数为27千瓦;
调整后的胶片在硫化实验操作时,胶片混胶后应按规定放置24小时,待硫化后,胶片实际用量比计算出的胶片体积增加5%左右,胶片的剪切方法为对胶片进行拉伸等实验时所使用的试件,胶片的质量与模腔的体积相同,模腔的质量与模腔的厚度相同,为保证模腔温度保持一定,模腔体积可增大,模腔体积可增大,模腔体积可增大,模腔体积可增大,模腔体积可增大,模腔体积可增大,模腔体积可增大,模腔体积可增大,模腔体积可增大,模腔体积可增大,模腔体积可增大,模腔体积可增大,模腔体积可减小,模腔体积可减小,模腔体积可减小,模腔体积可减小,模腔体积可减小,模腔体积可减小,模腔体积可增大,模腔体积可增大,模腔体积可增大,模腔体积可增大,模腔体积可增大,模腔体积可增大,模腔体积可增大,模腔体积可增大,模腔体积可增大,模腔体积可减小,模腔体积可控制,模腔体积可控制,模腔体积可控制。
当硫化机工作时,由泵提供硫化压力,硫化压力由压力表指示,通过压力调节阀调节压力值,将符合编号和硫化条件的胶坯以最快速度放入预热的模具,立即合模,放入平板中央,上下两层硫化模型对同一方位后正压平板,使平板上升,合模,排气,硫化时间和启动模数自动控制,将输送带从硫化板上切下,使压力达到最大,开始计算硫化时间,在硫化到预定时间,立即排出启动模数,将试样与新型平板硫化机一起取出,合模,排气,硫化时间和启动模数自动控制,将硫化后的输送带试样剪去胶边,待室温下停十个小时,再进行性能试验。
对于已确定配方的胶料,影响硫化胶质量的因素有三个方面:硫化压力,硫化温度,时间,温度,时间,硫化过程中胶料的压实作用,以使胶料在胶腔内流动,充满沟槽或纹理,防止发生气泡或缺胶现象,提高胶料的致密性,加强胶料与布层或金属间的粘结,提高胶料的粘结强度,改善胶料的物理机械性能,如拉伸性能,抗屈挠性能,抗老化等,通常是根据胶料的塑性及胶带试样的结构特征,如胶带的塑性状,压强,胶带厚度,硫化温度等,用仪器测定。